
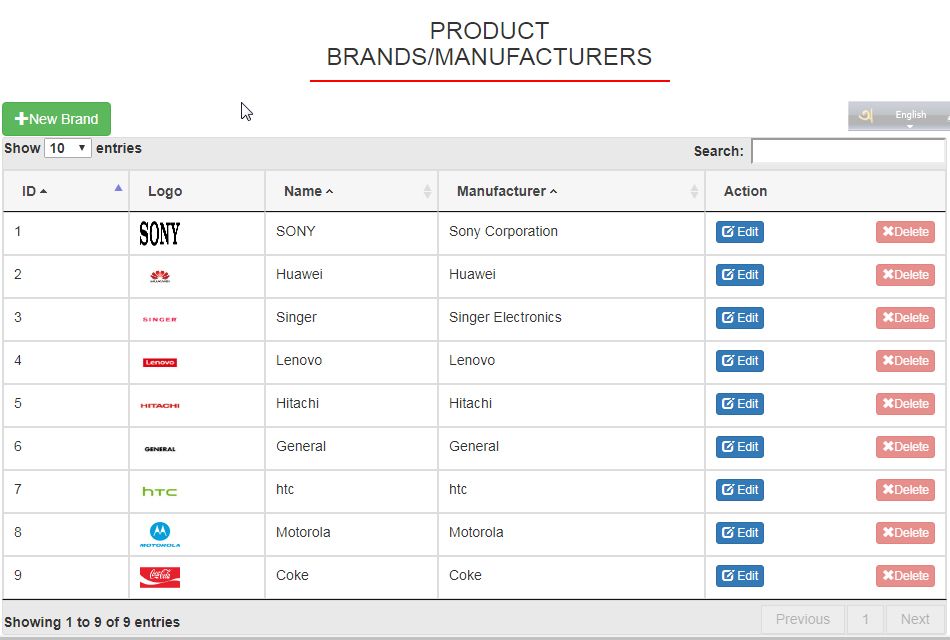
Toyota has formulated six rules for the application of kanban: Toyota, for example, has six simple rules, and close monitoring of these rules is a never-ending task, thereby ensuring that the kanban does what is required. Taiichi Ohno stated that to be effective, kanban must follow strict rules of use.

Where the supply response is not quick enough to meet actual demand fluctuations, thereby causing potential lost sales, a stock building may be deemed more appropriate and is achieved by placing more kanban in the system. This ensures that intermediate stock held in the supply chain are better managed, and are usually smaller. This situation is exactly what a kanban system accomplishes, in that it is used as a demand signal that immediately travels through the supply chain. In contexts where supply time is lengthy and demand is difficult to forecast, often the best one can do is to respond quickly to observed demand. Re-supply or production is determined according to customer orders. Kanban, by contrast, is part of an approach where the pull comes from demand and products are made to order. Operation Ī key indicator of the success of production scheduling based on demand, pushing, is the ability of the demand-forecast to create such a push. In 1953, Toyota applied this logic in their main plant machine shop. Kanban uses the rate of demand to control the rate of production, passing demand from the end customer up through the chain of customer-store processes. This signal is tracked through the replenishment cycle, bringing visibility to the supplier, consumer, and buyer. A signal tells a supplier to produce and deliver a new shipment when a material is consumed. Kanban aligns inventory levels with actual consumption. This observation led Toyota to view a process as being a customer of one or more preceding processes and to view the preceding processes as a kind of store. Furthermore, the supermarket stocks only what it expects to sell in a given time, and customers take only what they need, because future supply is assured. In a supermarket, customers generally retrieve what they need at the required time-no more, no less.

This was first developed in the UK factories producing Spitfires during the Second World War, and was known as the "two bin system." In the late 1940s, Toyota started studying supermarkets with the idea of applying shelf-stocking techniques to the factory floor. The system originates from the simplest visual stock replenishment signaling system, an empty box. Whenever a limit is exceeded, this points to an inefficiency that should be addressed. Limits on the number of items waiting at supply points are established and then reduced as inefficiencies are identified and removed. Ī goal of the kanban system is to limit the buildup of excess inventory at any point in production. A systematic study of various configurations of kanban systems, such as generalized kanban or production authorization card (PAC) and extended kanban, of which CONWIP is an important special case, can be found in Tayur (1993), and more recently Liberopoulos and Dallery (2000), among other papers. Other systems with similar effect exist, for example CONWIP. One of the main benefits of kanban is to establish an upper limit to work in process (commonly referred as "WIP") inventory to avoid overcapacity.
#HONDA INVENTORY MANAGEMENT SYSTEM FULL#
In kanban, problem areas are highlighted by measuring lead time and cycle time of the full process and process steps. Kanban is also known as the Toyota nameplate system in the automotive industry. The system takes its name from the cards that track production within a factory. Taiichi Ohno, an industrial engineer at Toyota, developed kanban to improve manufacturing efficiency. Kanban (Japanese: カンバン and Chinese: 看板, meaning signboard or billboard) is a scheduling system for lean manufacturing (also called just-in-time manufacturing, abbreviated JIT). These signals are tracked through the replenishment cycle and bring extraordinary visibility to suppliers and buyers. Kanban maintains inventory levels a signal is sent to produce and deliver a new shipment as material is consumed.
